I have don't think we have a dedicated thread for it yet so I will make one here. We have the compressor installed at the new Makerspace! Thank you again to Skeans Pneumatic and Automation for there donation of the compressor at the old space. It is continuing to serve us well.

Thank you to everyone who has helped with the install. Sorry if I miss anyone: Torsten, Grant, James and Andrew.
The compressor is in a small shack to the left of the woodshop exit. I poured a small slab, due to trying to get it done as soon as possible I took some shortcuts that defiantly burned me later. A shack was built off the building on the slab and insulated with Safe and Sound. The slab cracked, settled and would not take fasteners to hold the compressor. We placed ready rod in the holes and poured a new top on the slab. It is hardening well.
The compressor has been installed. It is on plywood pucks. It is on the 30 amp breaker on the low left of the panel. There is a valve on the wall by the lathe that will disconnect the compressor from the system. There is a dryer inline without he compressor. The drain from the dryer and the compressor tank are both attached to solenoids on timers and routed to blow out above the roof of the shack.
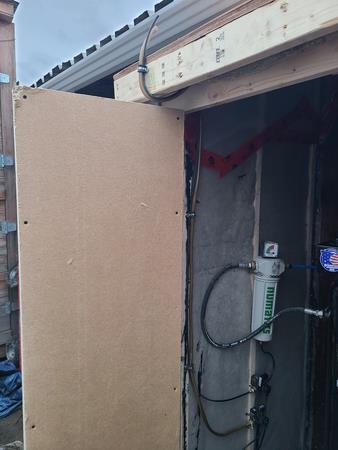
To do:
- Roof Shack
- 110 V for light and solenoids
- Heat
There is a lot more to add here. Please add any other documentation here so we have a future reference. Particularly the rest of the air system.